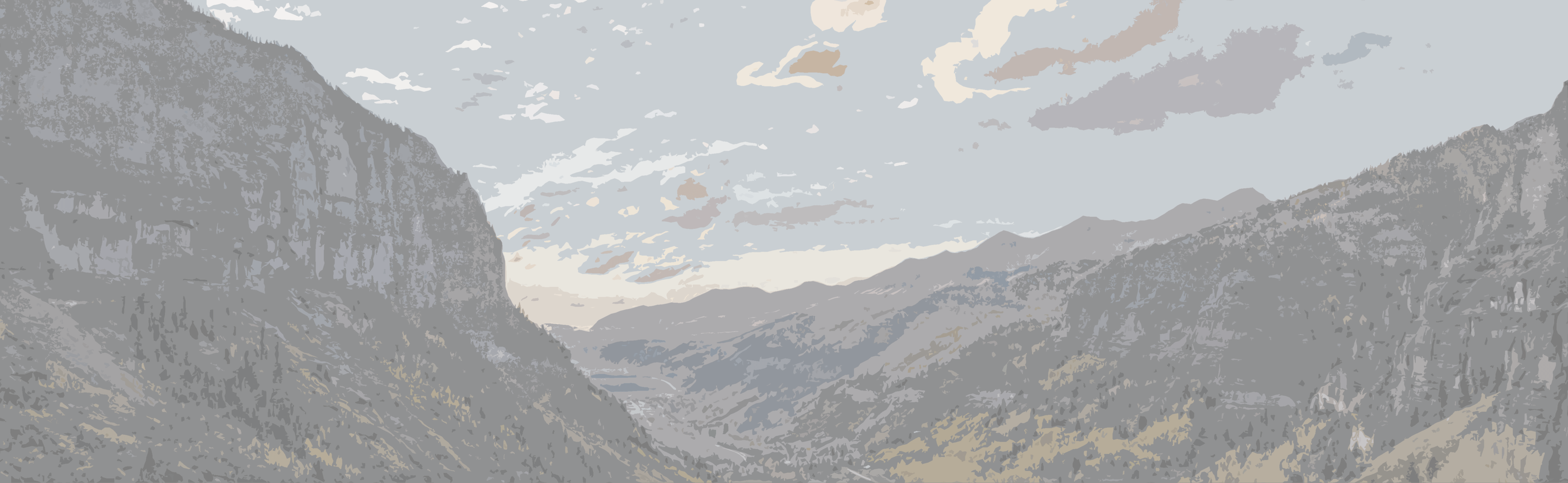
Our Skills
Telluride Engineering is a instrumentation & control, process safety and safety control system firm with an extensive background in manufacturing, operational technology, process engineering and control systems with a particular emphasis on the life sciences, semiconductor manufacturing and chemical industries.
Telluride Engineering has extensive experience in construction design for greenfield, brownfield, and process-specific construction. We offer full design services and will integrate into your design team and construction process, including 30/60/90/IFC print set packages, design verification, RFIs and other services during construction in the disciplines in which we’re skilled. We have licensed professionals in mechanical and control system engineering in AZ, CA, CO, ID, OR, NM, NY, TX, NC, PA and will gladly pursue licensure in any other state or location where it’s required for the success of your project. We’re well-versed in requirement generation and communication such as is required to monitor other disciplines’ equipment, or utilities that our systems may require to function. Telluride Engineering routinely engages in space planning, off-site manufacturing planning and design and other broad efforts required. Also, we have a broad tool install offering, including mechanical systems, controls systems and gas detection. Our primary focus is on the specialty services such as process chemicals, process gases, and the related controls, leak detection, and failure mode specifics to meet code and client-specific safety and design requirements.
Our robust understanding of system utility demands that ensures Telluride Engineering can help you quantify your facility’s opportunities for improvement for both existing and new facilities. We can help you evaluate equipment replacement and upgrades for a given ROI, add control systems to shut equipment down when not in use, and leverage utility contracts and options to reduce overall rate structure. Considerations include, but are not limited to: irrigation systems, HVAC, pumping energy, process water consumption, heat pumps, geothermal systems, solar systems, high efficiency chillers, LED lighting, aging equipment.
Safety control systems, which include a broad range of different systems depending on application, industry and authority having jurisdiction (AHJ) are generally a separate and independent layer of protection from the basic process control systems (BPCS). This allows the process to remain in a safe state in the case of a failure of the BPCS. Telluride Engineering can help design both, taking a formal process safety and risk-based approach to them, ensuring they remain independent layers of protection without credible common-cause failures.
Our personnel have partnered with trusted conventional life safety systems/fire alarm design firms in the past to deliver design and construction service in facilities. We can identify the specific demarcation between hazards managed by the LSS, and hazards managed by the SIS (or TGMS/HPM-LSS). For large cleanroom spaces, other areas with particularly challenging contours and ceiling configurations or when detection of a fire event in the incipient stage is warranted by life safety or property protection purposes, we can help with the introduction of active smoke detection, air sampling smoke detection/early warning (ASSD/EWSD, and sometimes seen under the trade name “VESDA”).
Due to our process engineering background, we can generate datasheets, develop sequences of operations, P&IDs, PFDs and cause and effect matrices to develop a robust control strategy for your process. We can develop control strategies both from a process control standpoint, and from the perspective of safety systems.
Telluride Engineering has a background the unique gas and chemical distribution systems required for manufacturing. This includes some notable systems such as high purity, toxic and flammable gases, and similarly specialized chemicals required in the chemical-heavy manufacturing industry. We can help design double-contained piping, leak detection, and specialized delivery systems to meet both the process and safety needs.
Safety Instrumented Systems, implemented as result of a process safety assessment, and an integral role of process safety management (PSM) are computerized independent control systems design to safeguard against hazardous outcomes in the event of a failure. They are generally comprised of safety instruments (such as temperature sensors, level switches, and pressure sensors) and safety control devices (such as an isolation valve or shutoff relay). The advantage of a PLC-based safety instrumented system over traditional fail-safe wiring is the ability to generate a safe state other than shutdown. For example, if a process becomes more hazardous by shutting down in incoming neutralizing chemical, an SIS could make the informed decision to leave it running while shutting off other elements of the system generating the hazard.
These systems, generally designed under the guidance of IEC 61508 and 61511, are rated for reliability using SIL (safety integrity levels 1-3) or PL (performance levels a-e) with different cost and capabilities based on specific requirements of a system, consequence of hazard and overall risk thresholds. The SIS’s benefits are most significant when performed during the initial process design and scoping phases.
Telluride Engineering has a TÜV Rheinland Functional Safety engineer certified in safety instrumented systems and process hazard & risk assessment on staff, and can provide an SIS design either in tandem with a BPCS design, or in addition to a 3rd party design or as an addon to an existing BPS. We can also help quantify the risk.
A subset of the SIS, and somewhat a of a misnomer because it’s responsible for much more than just toxic gases, TGMS/HPM-LSS is frequently seen in the semiconductor industry. Telluride Engineering has robust knowledge of TGMS/HPM-LSS design within the semiconductor market segment. We can develop a TGMS/HPM-LSS system from the ground up, including all controls, gas detection and communication equipment. From a list of gases and chemicals relevant to the site, we can further determine quantity, position, placement, detector family and type. Ambient detection both indoor and outdoor are particularly challenging because of the number of elements that can drive change. Further, we’re skilled in integrating the site TGMS/HPM-LSS to vendor equipment, HVAC equipment (typically through the BPCS/I&C system) or other notification consoles and spaces.
Industrial Control Systems, sometimes referred to as instrumentation and control (I&C) or basic process control systems) are the backbone of any plant or factory’s operations. We can design control systems and endpoint instrumentation for all control systems, with significant experience in the current Rockwell and Siemens hardware offerings. Telluride Engineering’s emphasis on safety puts us in a unique position to be able to design both the BPCS and SIS or other safety control system for the factory, in addition to specialized process engineering controlled by these systems. We have experience in industrial and commercial/building network design (such as the physical copper and fiber) and network topology, configuration and systems planning aspect. We further have a background in Windows and Linux server and workstation support, and multiple other systems, which we can leverage to ensure the system is ready for ultimate integration and startup. We can consult in and provide management services for supervisory control and data acquisition (SCADA) and PLCs.
We have extensive experience in gas and chemical system design, including piping, double containment, high purity piping, stainless and gas detection and chemical detection and leak monitoring. This includes gas and chemical distribution infrastructure such as distribution valve boxes (DVBs), valve manifold boxes (VMBs), gas cabinets, gas concentrators and purifiers for on-site generation, chemical tanks, blenders and similar specialty equipment. We also design on the chemical side, including integration of vendor equipment to the facility, stick-built equipment on site, and ultimately integration of the gas and chemical supplies into the tools.
Our team is also skilled in project management for upgrades, new construction or other changes required for your facilities.